The Importance of Pump Seals in Industrial Applications
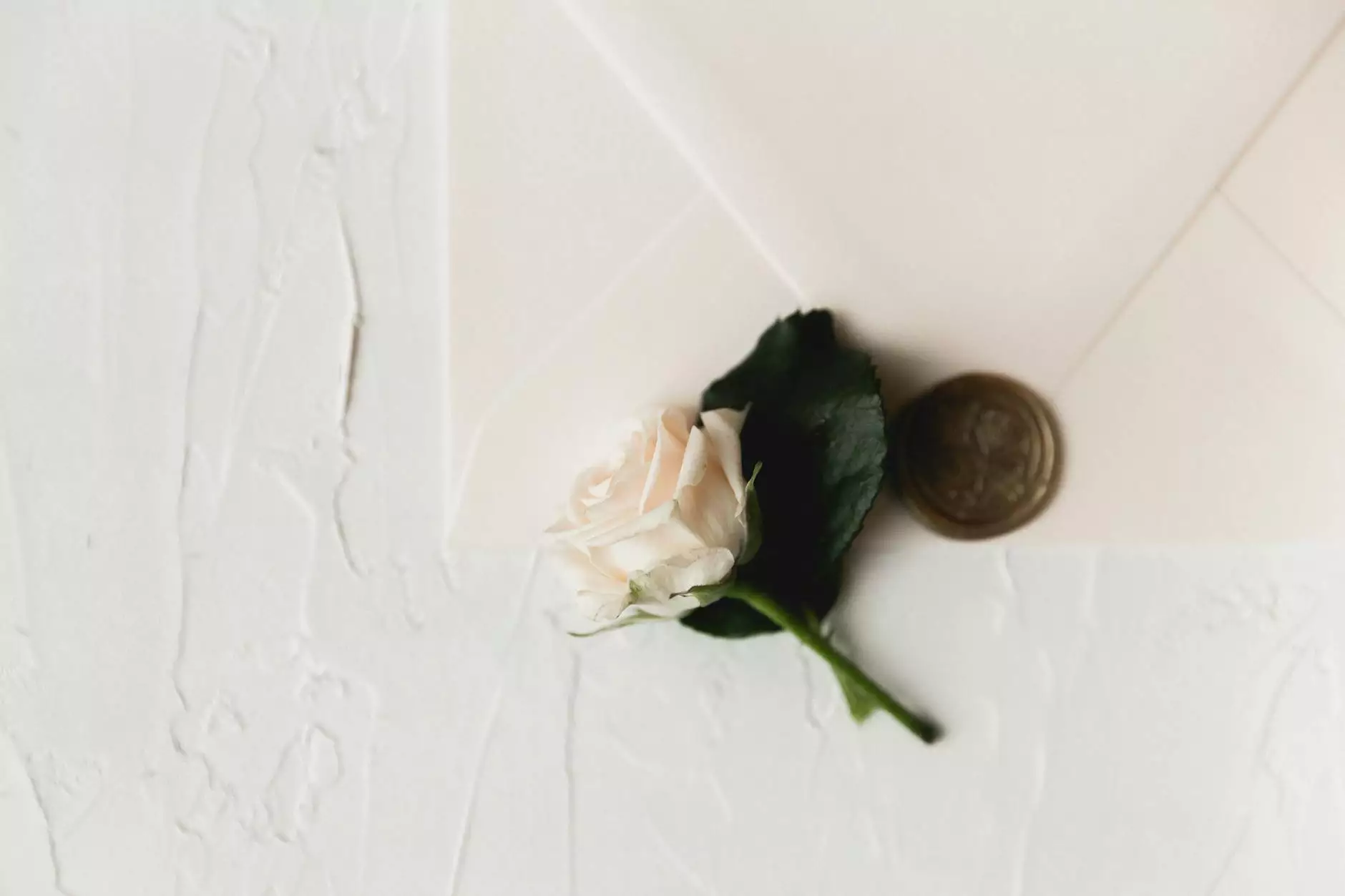
When it comes to industrial applications, pump seals are among the most critical components that ensure the efficient operation and longevity of pumps. Whether you're involved in auto repair, farm equipment maintenance, or structural engineering, understanding the intricacies of pump seals can significantly enhance your operational capabilities.
What is a Pump Seal?
A pump seal is a mechanical device designed to prevent fluid leakage at the junction where a pump shaft passes through its housing. They play a crucial role in ensuring the proper function of pumps by containing liquids or gases, reducing the risk of contamination and maintaining efficiency. They come in a variety of materials, styles, and configurations, tailored to meet the specific demands of various industrial sectors.
Types of Pump Seals
There are several types of pump seals that you may encounter in your business operations:
- Mechanical Seals: Commonly used in centrifugal pumps, these seals consist of two main components: a rotating part and a stationary part, which work together to prevent leakage.
- Gasket Seals: These seals are used to fill the space between two surfaces, preventing leakage. Gaskets can be made from various materials, including rubber, cork, and paper.
- O-Ring Seals: Simple yet effective, O-rings are round elastic rings that, when compressed, form a tight seal in a wide array of applications.
- Lip Seals: Often used in rotary applications, these seals feature a flexible lip that makes contact with the shaft while preventing the escape of lubricants.
- Packing Seals: Comprising braided fibers, packing seals are used in a variety of pumps and are particularly effective at sealing around rotating shafts.
Why Pump Seals are Essential for Your Business
Investing in high-quality pump seals is essential for any business involved in auto repair, farm equipment repair, or structural engineering. Here are several reasons why:
1. Prevention of Leakage
Leakage can lead to significant operational costs, environmental damage, and safety hazards. Pump seals effectively contain fluids, minimizing the risk of spills and leaks, which can save a company from hefty fines and cleanup costs.
2. Enhanced Efficiency
Well-functioning seals ensure that pumps operate at optimal efficiency. When pumps run smoothly, they consume less energy and require less maintenance. This leads to reduced operational costs and increased profitability.
3. Minimization of Downtime
Downtime due to pump failures can cripple a business. High-quality pump seals contribute to the reliability of pumps, leading to less frequent breakdowns and repairs. This means that your business can focus on what it does best, rather than constantly addressing equipment issues.
4. Safety Compliance
Many industries are governed by strict safety regulations regarding fluid containment. Using high-quality pump seals helps businesses comply with these regulations, avoiding legal issues and enhancing workplace safety.
Choosing the Right Pump Seal
Choosing the right pump seal for your application is vital. Below are some key considerations:
- Material Compatibility: Ensure the seal material is compatible with the fluids being pumped. For instance, harsh chemicals require seals made from robust materials like PTFE.
- Temperature Resistance: Pumps involved in high-temperature applications require seals that can withstand elevated temperatures without degrading.
- Pressure Ratings: Evaluate the pressure conditions under which the pump operates. The chosen seal must withstand these pressures without failing.
- Chemical Resistance: The selected seal should be resistant to any chemicals that might come in contact with it, maintaining integrity and functionality.
Maintenance Tips for Pump Seals
To ensure the longevity and effectiveness of pump seals, regular maintenance is essential. Here are some tips:
- Regular Inspections: Schedule routine inspections of pumps and their seals to detect any early signs of wear or damage.
- Monitor Fluid Levels: Keep an eye on the fluid levels in your pumps; low levels can lead to overheating and seal failure.
- Check for Leaks: Regularly check for leaks around pump seals, as this can be an indicator that a replacement is needed.
- Replace Worn Seals Promptly: Do not delay in replacing worn or damaged seals, as they can lead to more significant issues in the future.
Case Studies on Pump Seal Effectiveness
Many businesses have experienced significant improvements by upgrading their pump seals. Here are a few case studies:
Case Study 1: Auto Repair Shop
An auto repair shop reported reducing its operational costs by 30% after switching to high-performance mechanical seals. The improved reliability of their equipment led to fewer breakdowns, enabling them to handle more customers efficiently.
Case Study 2: Agricultural Equipment Manufacturer
A farm equipment manufacturer faced excessive downtime due to pump failures. After implementing high-quality gasket seals, they saw a 50% reduction in maintenance calls, boosting their operational efficiency and profit margins.
Case Study 3: Structural Engineering Firm
A structural engineering firm that regularly used high-pressure pumps in their projects upgraded to advanced lip seals. This change resulted in significant time savings and compliance with safety regulations, enhancing their reputation in the industry.
Conclusion
In conclusion, understanding the importance of pump seals in your business operations—whether related to auto repair, farm equipment maintenance, or structural engineering—is crucial for optimizing efficiency and cutting costs. Prioritizing the selection, installation, and maintenance of these essential components can lead to tremendous benefits and enhance the overall performance of your equipment.
By focusing on high-quality pump seal solutions, your business can avoid unnecessary downtime, cut operational costs, and ensure compliance with safety regulations. Remember, investing in reliable pump seals today will pay dividends in the long run.