Injection Mold Plastic: Revolutionizing the Metal Fabrication Industry
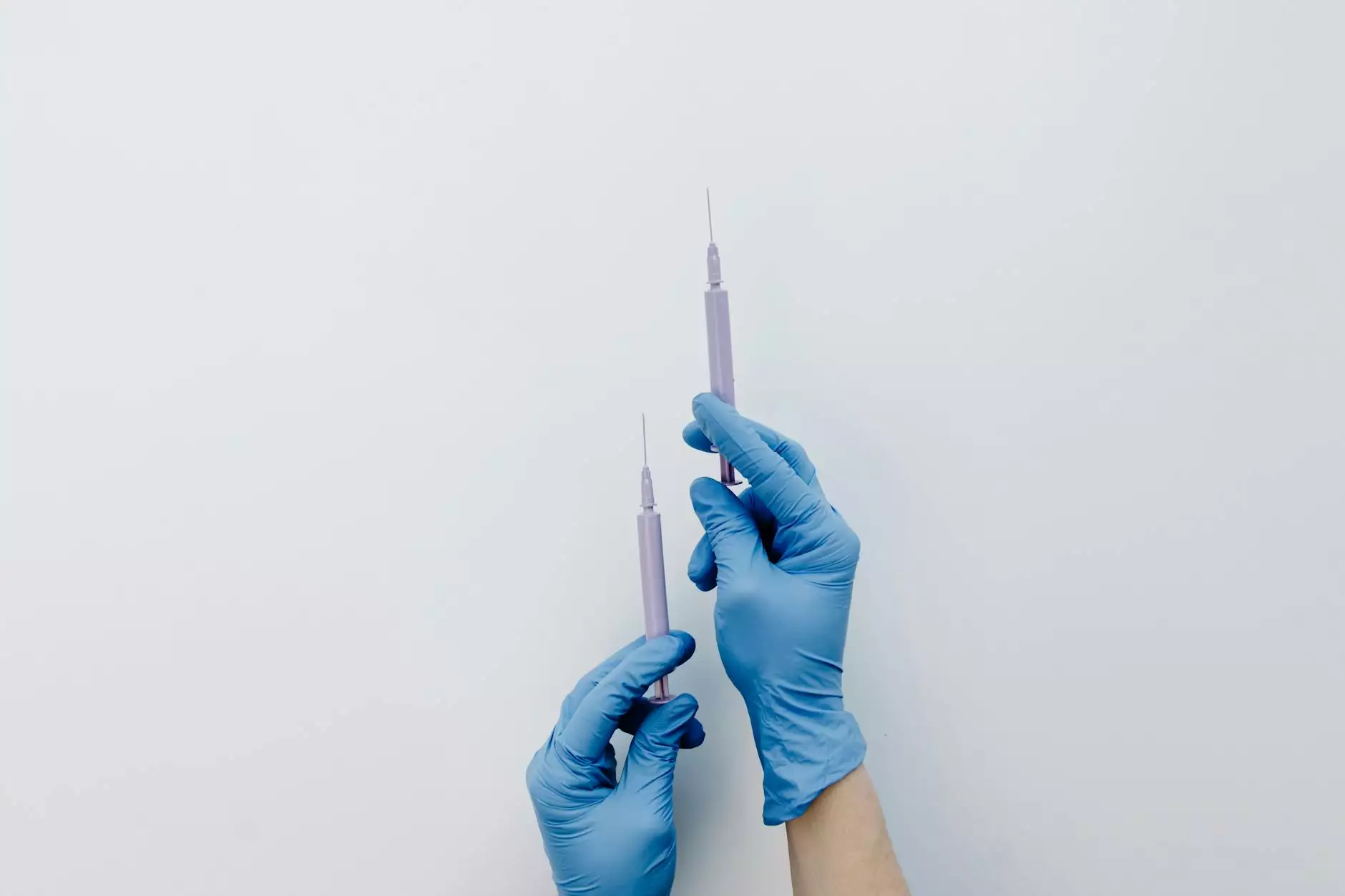
In the ever-evolving world of manufacturing, injection mold plastic has emerged as a game-changer, particularly within the realm of metal fabrication. This manufacturing process not only enhances efficiency but also provides unparalleled precision in producing complex parts. In this article, we will delve deep into the intricacies of injection molding, its advantages, applications, and how it fits seamlessly into the framework of metal fabricators like deepmould.net.
Understanding Injection Mold Plastic
Injection molding is a process that involves the injection of molten plastic into a mold to form a specific shape. This method is widely utilized for producing a diverse range of plastic components, making it a preferred choice for metal fabricators seeking to integrate plastic parts into their operations. The materials used in injection molding are often thermoplastics, which can be remelted and reshaped multiple times, thus promoting sustainability and reducing waste. Here are some key characteristics of injection mold plastic:
- Versatility: Injection molded plastic can be tailored to meet various specifications, making it suitable for numerous applications.
- Durability: Products made from injection mold plastic are known for their strength and resistance to wear.
- Cost-Effectiveness: Mass production capabilities lower the unit cost significantly, making it economical for businesses.
- Design Flexibility: Intricate designs and complex geometries can be achieved, enabling innovative product development.
The Injection Molding Process
The injection molding process comprises several critical steps, each contributing to the final product's quality and efficiency:
1. Material Preparation
Before molding can begin, the selected plastic material must be prepared. Pellets of plastic are first dried to remove any moisture, which could adversely affect the quality of the final product. Proper drying is key to achieving optimal strength and appearance.
2. Melting the Plastic
The dried plastic pellets are then fed into an injection molding machine where they are heated until they become molten. The temperature is meticulously controlled to ensure that the plastic maintains the right viscosity for effective filling of the mold.
3. Injection into the Mold
Once the plastic is molten, it is injected at high pressure into a precisely designed mold. This ensures that every nook and cranny of the mold is filled, creating an accurate replica of the desired part.
4. Cooling
After the injection, the plastic must cool and solidify within the mold. This step is crucial as it determines the part's final strength and dimensional accuracy. Cooling time varies depending on the thickness and complexity of the part.
5. Ejection
Once cooled, the mold opens, and ejector pins gently push the newly formed plastic part out of the mold. This step must be performed carefully to avoid damaging the part.
Advantages of Using Injection Mold Plastic in Metal Fabrication
The integration of injection mold plastic in metal fabrication offers numerous benefits that can enhance product quality and operational efficiency:
- Reduced Weight: Substituting metal components with injection molded plastics can significantly decrease the overall weight of a product, leading to enhanced performance and fuel efficiency in applications like automotive manufacturing.
- Enhanced Design Opportunities: The flexibility in design allows for more creative and functional solutions that simply cannot be achieved with traditional metal fabrication methods.
- Improved Corrosion Resistance: Many plastics possess inherent resistance to corrosion, ideal for industries such as aerospace and maritime.
- Faster Production Times: The quick cycle times of injection molding facilitate rapid production, allowing businesses to meet tight deadlines and react swiftly to market changes.
Applications of Injection Mold Plastic in Metal Fabrication
Injection mold plastic finds its application across various sectors, enhancing products and processes in numerous ways. Some notable applications include:
1. Automotive Industry
In the automotive sector, injection molded plastics are used to create parts such as dashboards, bumpers, and interior trim. The ability to produce lightweight and robust components contributes significantly to vehicle efficiency and performance.
2. Consumer Electronics
Consumer electronics rely heavily on injection molding for creating enclosures, buttons, and various intricate components. This manufacturing method ensures that parts are not only aesthetically pleasing but also functionally viable.
3. Appliances
Home appliances benefit from injection mold plastic as it allows for the production of durable and stylish components that meet consumer demands while ensuring longevity.
4. Medical Devices
In the medical field, precision and safety are paramount. Injection molded plastic parts, such as housings for medical instruments and devices, ensure compliance with strict regulatory standards while minimizing weight and manufacturing costs.
Choosing the Right Injection Mold Plastic for Your Needs
When it comes to selecting the appropriate injection mold plastic for your project, several factors must be considered:
- Material Properties: Evaluate the mechanical, thermal, and chemical resistance properties of the plastic to determine its suitability for your application.
- COST: Balance between quality and budget to ensure that you achieve the best results without overspending.
- Compatibility with Metal Parts: Ensure that the chosen plastic integrates well with any metal components to maintain structural integrity.
- Production Volumes: Consider the expected production volume, as some materials might be more cost-effective for large-scale production than others.
The Future of Injection Mold Plastic in Metal Fabrication
As technological advancements continue to unfold, the future of injection mold plastic in metal fabrication looks promising. Innovations such as 3D printing and computer-aided design (CAD) are significantly influencing the development of new materials and processes that will enhance the capabilities of injection molding.
Moreover, the push for sustainability is prompting manufacturers to explore biodegradable and recycled plastics, providing environmentally friendly alternatives without sacrificing performance. The emphasis on lightweight materials, especially in the automotive and aerospace sectors, will further drive the adoption of injection mold plastics.
Conclusion
In summary, injection mold plastic is a crucial element in the landscape of modern metal fabrication. Its versatility, efficiency, and ability to produce high-quality components make it an invaluable resource for manufacturers. Understanding its processes, benefits, and applications empowers businesses to leverage injection molding effectively, enhancing their manufacturing capabilities while meeting the demands of today's market.
For companies seeking to innovate within the realm of metal fabrication, including deepmould.net, embracing injection mold plastic can lead to remarkable advancements and sustained competitive advantage. The integration of modern plastics is no longer just a trend; it is a vital component of a successful manufacturing strategy.